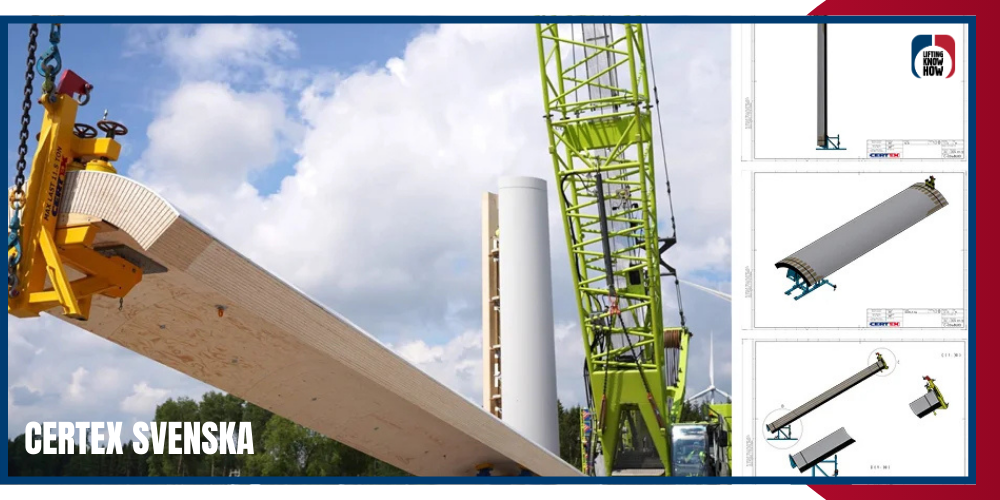
A 105-meter-tall wind turbine made of wood—the tallest of its kind in the world. It may sound futuristic, but thanks to Modvion’s groundbreaking technology and CERTEX Sweden’s engineering expertise, it’s now a reality. Adam Johansson, construction manager and responsible project leader, talks about a mission where the team at Special Products in Sweden created a unique lifting solution.
Traditionally, wind turbines are made of steel or concrete. However, as part of the green transition, Modvion is pioneering prefabricated wooden towers—cutting carbon emissions by at least 25% during production. The lower weight of wood and the modular concept mean the towers can be built higher and transported on public roads. Laminated wood is also stronger per unit of weight than steel.
Raising and lifting the 14.6-meter long and 11.5-ton heavy modules on-site requires experts with the right equipment. In other words: a perfect job for the CERTEX team, where high competence and lifelong experience with specially designed lifting yokes and lifting equipment are a trademark.
"Innovative thinking and finding smart solutions are our strengths. Additionally, we have full control over guidelines, regulations, and directives, which means we always deliver products that are both tailored to the customer's specific purpose and comply with all applicable laws and safety requirements," says Adam Johansson.
Custom-made Cradle
A specific requirement from the client Modvion was that no marks could be made on the sections, which required extensive calculations to ensure good safety margins in relation to the maximum surface pressure. To succeed with the project, two central components were designed – a “cradle” and a custom-made lifting device.
The function of the cradle was to align the modules at the correct angle before lifting, and it was designed to match both the angle and the conical shape and inclination. The lifting device was then to be connected and locked onto one section at a time with a predetermined lifting point on the inside. Wood protection was mounted on the tool to match the module's inner shape. The lift itself was then carried out using a mobile crane connected to the lifting device.
"To protect the sections, we decided to use rubber pads, which also had to be custom-made. When we were creating these protective cushions, we contacted and collaborated with a consultant who is an expert in rubber," says Adam Johansson.
Test Loadings with Twice the Maximum Load
Before the wooden modules could be lifted into place, test loadings of the lifting device were carried out with specially designed fixtures at CERTEX's test facilityto ensure the strength of the device under the various loads it would be exposed to in real life.
"We physically test all our lifting devices with twice the maximum load. In this case, it was an extensive task and a tricky project – which we, of course, solved," says Adam Johansson.
The most exciting part of the entire project was raising the modules, both in terms of shape and material, he says.
"They are large, heavy to lift, and made in special shapes. At the same time, they had to be lifted with precision without being damaged and then glued in place. The lifting angle could not deviate; otherwise, there would be too much stress on the tool."
Through good collaboration and dialogue with Modvion, CERTEX managed to realize their vision. The 105-meter-tall wooden tower is now on display outside Skara. The inauguration took place in early March 2024, and the wind turbine, owned by Varberg Energi, is already running, and producing green electricity.
Watch the video here.